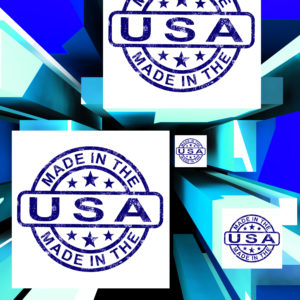
Why U.S. Manufacturing Is On the Rise
Manufacturing trends in the United States look very promising. In the last few months, the manufacturing sector in the country has seen a higher growth than what the sector experienced in the last couple of years. This truly is an optimistic sign, as it is an indication the U.S. manufacturing is once again on the rise. There is hope the country’s economic recovery is around the corner. But what are the reasons for the sudden rise? (more…)