Medical supplies. Food. Due to COVID-19, both are in extremely high demand and will be for the foreseeable future, making medical- and food-grade plastic injection molding extremely busy industries.
How busy? Back in March, Forbes reported that the Director General of the World Health Organization called on global manufacturing of medical masks, gloves and goggles to increase by 40%. Also critical, as the same article noted: nylon-plastic swabs for testing kits, plastic vials for testing kits, and ventilators. Fast forward to early May, when vaccine developments started circulating. As the New York Times noted, more than 300 million people may need a coronavirus vaccine in the United States alone, making the production of the items necessary to deliver a vaccine extremely essential.
Equally in demand is food-grade packaging. In the midst of COVID-19, it all ties back to safety. Single-serve products help minimize cross-contamination. Plastic-contained bites keep the virus on the surface of the container, minimizing the risk of coronavirus getting into the food and therefore into someone’s body. Restaurants are only open for carry-out to promote social distancing, requiring appropriate to-go containers.
All this adds up to an increased need for medical- and food-grade plastic injection molding. To step up and help meet this demand, there are three things you and your team can focus on: production efficiency, scrap reduction and startup.
Maximizing Injection Molding Production
To make your runs as productive as possible, you need to release as many products as you can while minimizing downtime. Applying a nano-thin coating when the mold is out of the press, like HCF™ Heat Cure FDA Compliant, is a good first step. It offers extraordinary release, up to 300,000 cycles, and eliminates the need for traditional mold releases that build up and require shut down for cleaning.
Minimizing Scrap
If you use a grease that doesn’t break down, you’ll significantly minimize, and possibly even eliminate, scrap from bleeding into the mold cavity, injector pins, and other areas. Applied correctly, Syn-Lube™ (high temperature, high performance, synthetic grease) and Cera-Lube™ (high performance, nano ceramic grease) mitigate bleed off. Both remain on the surface longer than PTFE lubricants, extending production time up to ten times longer. In fact, Syn-Lube helped one manufacturer go from 1,000-1,500 parts per day, to 24,000 parts, with the product lasting weekly versus daily.
Speedier Startup
When it comes time to store your molds, use a dry rust preventative, like Safe T Guard™. Unlike other rust preventatives that claim to be dry, Safe T Guard truly is, so it won’t break down grease and can be molded through at startup, getting your production up and running faster and reducing scrap significantly.
If the onset of COVID-19 and related quarantine orders didn’t give you time to properly store and maintain your molds, a cleaner like Zap-Ox™ will have them back in operating form ASAP. Zap-Ox cleans gassing and burn marks, buildup, and more with little-to-no scrubbing, saving maintenance and downtime.
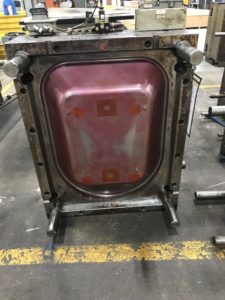
Before using Nanoplas Zap Ox
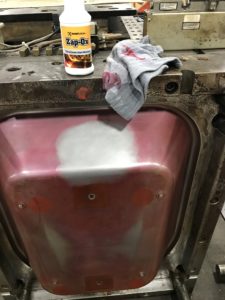
Coming clean with Nanoplas Zap-Ox
Note that all Nanoplas products mentioned above are FDA-compliant or NSF-registered, making them appropriate for medical and food-grade plastic molding.
Whether you increase production by focusing on one, two, or all three of the areas discussed, or are trying to maintain the same output with less staff due to health and safety measures, we here at Nanoplas want to help, so don’t hesitate to contact us. We’re happy to provide a free sample, product recommendation, or answers to any questions you might have.