by Admin | Jun 3, 2015 | Manufacturing, Recent Posts |
How SMED and Mold Maintenance Work Together
Time is money in the production business and the more you waste, the more you lose. The Single-Minute-Exchange of Die (SMED) methodology may allow you to successfully implement a lean production process in your injection molding business, and when combined with a progressive mold maintenance program, allow you to reduce the time needed for changeovers.
Why Lean?
Lean manufacturing aims to eliminate unnecessary waste during production, and uncovering ways that will add value by eliminating or decreasing other processes or variables than can adversely effect production.
With the rising cost of transportation and raw materials, it has become increasingly important for injection molders to produce a wide variety of products. With that product expansion, the need for efficiencies and cost reductions has generated a lot of interest in the lean method.
Potential Problems in High Variety Production
- Lengthy and difficult set up procedures.
- Expensive, high-tech machines are required to increase production capacity and flexibility.
- Waste arises out difficult changeovers, lack of adequate maintenance or equipment not being ready when needed.
SMED (Single-Minute-Exchange of Die and Maintenance
Globalization and Just-In-Time models have increased the need for production of smaller lots on a more frequent basis. This shift in format requires accelerated set-ups to maintain flexibility, to meet customer demands, and to remain competitive.
SMED allows you to make the necessary reductions in changeover time to achieve a just-in-time pace. The practices under this system achieve machine changeover in less than 10 minutes (single digit minutes) thus reducing the time during which production is down. The SMED approach does not only just reduce changeover times but also the overall labor involved.
The goals of SMED are:
- Reduction in inventory
- Reduced changeover time
- More efficient changeover process
- Flexibility for reduced batch/lot size
- Improve flexibility in equipment usage
- Reduce impact and downtime on equipment
- Meet customer demand
SMED Process
SMED involves certain steps, with a basic overview as follow:
- Elimination of Non-Essentials: Observe and record the areas where change outs are required, then eliminate all non-essential activities where possible, especially duplication. By eliminating non-essential activities it is possible to speed things up and reduce waste.
- External Set-up: Get all the materials and supplies to be used in place so that they are available when required. Some things to consider for this include: color code all items needed, create checklists and develop and maintain uniform standards and procedures
- Internal Set-up: Replace complex tools where possible with more simple equipment to prevent unnecessary waste. Use functional jigs and fixtures, levered or one-turn fasteners, preset guides, pins and notches. Remember the goal is to work efficiently but still but also effectively.
- Measure: The SMED approach entails change, but to know if you’re on the right track it is vital to measure business performance every time. It is a successful way of knowing if improvements are being made or not. Based on the results obtained, corrective or proactive measures can be taken. Consider the time lost/wasted as the benchmarks you will need to improve upon.
Benefits of Equipment Maintenance
The SMED system also requires proper maintenance of tools and equipment. When equipment is well looked after, it is more reliable. It will result in production efficiencies and lower costs due to fewer breakdowns and equipment downtimes. Also, with an effective maintenance program, equipment required will be available as and when necessary reducing wasted time and high costs due to idle equipment and staff.
It is also imperative that molds are stored properly to ensure optimal performance and longevity. Instead of leaving it on the floor or on pallets where it can sustain damage, it is best to store molds in a designated storage area or if possible on shelving or racks. Furthermore, it is best to use rust preventatives and grease that require little or no pre-production cleaning for start-up.
Many companies treat mold maintenance as an after thought, and have yet to explore how new products (like the Nanoplas line of mold maintenance products) can have a significant impact on their set-up and speed to press times. These gains in production efficiencies when combined with an approach like SMED can have a real impact on the bottom line.
To learn more about how the integrated family of Nanoplas products can help reduce scrap, increase production efficiencies and save time for your injection molding operation, contact us today!
by Admin | Sep 2, 2014 | Uncategorized |
This is the final installment in a series on flash free molding. [Read Part 1 and Part 2.] In this article, we will get into issues with tool design with shut-offs, parting line maintenance, and where the machine can contribute to flash. First, I would like to briefly go over how to define flash. Flash at times can be difficult to eliminate, and many will give up and accept this defect. Flash also can be miss-diagnosed at times with miss-matched parting lines or feather flash. I have seen miss-match called flash many times, but if it is flash you can see or feel it from both sides, miss-match will only be seen or felt from one side. (more…)
by Admin | Sep 2, 2014 | Uncategorized |
I hope you found the first article on flash free molding interesting. [Read Flash Free Molding Part 1.] I covered cavity pressure versus clamp pressure and will talk tool deflection in this article. Tool design and construction can be a contributor to flash issues. But, if you read the first article and the three conditions are met, flash is not possible. An inadequate tool design can contribute to flash by allowing deflection in line with clamp force and perpendicular to clamp force. Also, on the construction side, improper spotting, timing of components, and fitting of components can be contributors to flash. (more…)
by Admin | Jul 17, 2014 | Plastics, Recent Posts |
Cold Runner Vs. Hot Runner Molding Systems
Why should you choose a hot-runner mold system over a cold-runner mold system (or vice versa)? Each type of molding system has unique features that help determine exactly which one is best for you.
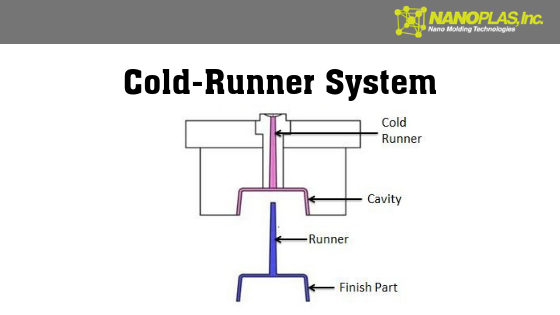
Cold-Runner Mold Systems
Called a cold-runner mold system because the runners are the same temperature as the molds, there are two types of cold-runner systems: a three-plate system and a two-plate system.
Three-plate systems allow the part to be ejected from the runner without an ejection system, but are a little more complicated than a two-plate system, which does require an ejection system to remove the part and the runner from the mold. Two-plate systems can handle most molds, however a three-plate system is friendlier when it comes to complex designs.
In a cold-runner mold system, the runner has to be larger than the part. Otherwise, you run the risk of underfilling the mold. One big advantage over a hot-runner system is the ability to use more types of polymers without concern for heat sensitivity.
Cold runners are less expensive than hot runners and are easily maintained as well, but they can create waste unless you can recycle or melt down the extra material.
Pros and Cons of Cold Runner System
Pros
- Inexpensive
- Few restrictions on types of polymers
- Easy to maintain
- Easy to change colors
Cons
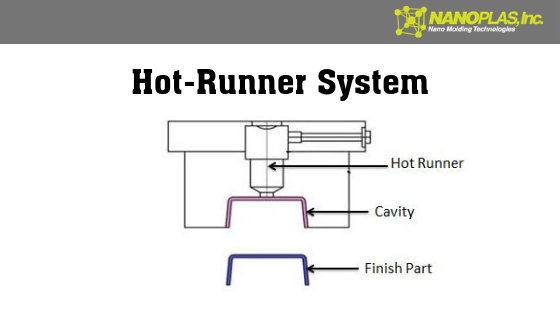
Hot-Runner Mold Systems
There are two types of hot-runner mold systems, both of which use two plates heated by a manifold system. Externally heated molds allow you to use more heat-sensitive polymers while internally heated molds generate better flow control. Depending on your materials and applications, you may prefer (or need) one type over the other.
Hot runners are more expensive than cold runners (in initial investment and maintenance), but they can handle higher volumes and larger parts and also don’t generate any waste. In some cases, the lack of waste balances with the higher maintenance cost to actually be about the same net cost as a cold-runner system.
Overall, hot-runner molds produce parts with more consistent quality and do so with faster cycle times, but it’s not as easy to change colors nor can hot runners accommodate some heat-sensitive polymers.
Pros and Cons of Hot Runner System
Pros
- Fast cycle time
- Consistent quality
- Very little waste
- Ideal for larger parts and higher volumes
Cons
- Expensive to purchase and maintain
- Not ideal for some heat-sensitive polymers
- Difficult to make color changes
Which System is Right for You?
Depending on exactly what you’re doing with your molds—materials, applications, size, volume, etc.—you may have a clear answer as to the best mold system or it may be more complicated. For instance, if you’re only working with heat-sensitive polymers, a cold-runner mold system is probably your best choice. If you’re producing large volumes and need faster cycle times, you’re probably looking for a hot-runner mold system.
However, those aren’t definite answers and shouldn’t be taken as such. You need to consider every facet of what you’re doing to determine the best system for you. Feel free to contact us if you’d like to talk about which type of mold system is your best option.
by Admin | Jul 16, 2014 | Recent Posts |
From Kaysun Corporation, a great piece on the injection molding process: Injection molding is a dynamic, complex process that requires testing and usually some adjustments to get it to perfection. It’s not an exact science, but some manufacturers focus on the specifications of the mold first and then build the process around the finalized mold, hoping this saves time and money. This approach, however, often results in production problems, slowing the whole process down and reducing the quality and repeatability.
“The best approach is developing a consistent, efficient process first, followed by fine-tuning the mold to the process.”
Read the full article HERE.