by Nanomold Coating | May 29, 2020 | Recent Posts |
Easy Solutions to Splay Caused by Bleeding
Undesired bleed out in injection molding can be caused by—and lead to—a number of problems. One of the most common injection molding defects caused by bleeding is splay, which is often the result of an over-lubricated mold
Syn-Lube™, which breaks down differently than other greases and helps eliminate bleeding, when applied properly, could be the solution to any issues you’re experiencing with splay.
What is Splay?
Silver or white streaks appearing on the surface of the part often indicate splay in injection molding. Several other defects, like scuffs, flow lines, surface scratches, delamination from contamination and flaking, can resemble splay, so it’s important to determine the cause of the streaks as the first step in troubleshooting.
When the cause is from bleeding, you’re probably looking at splay, potentially from a mold with too much lubricant or grease.
How Bleeding Can Cause Splay
If the splay shows up immediately after getting the mold from the tool room, it’s likely the result of too much grease being applied to the mold. When a mold is over-lubricated, grease from the lifters and ejector pins may bleed onto the surface of the part, which then leave the silver or white streaks indicative of splay.
Sometimes, grease can get trapped in the mold inserts, which also leads to bleeding out.
More is not better when it comes to lubricating a mold, so it’s important to know how to properly apply a grease (see bottom of the page for instructions).
Using Syn-Lube to Mitigate Bleeding
The proper application of any lubricant is essential. Even better: the proper application of Syn-Lube. Syn-Lube high-performance synthetic grease lasts 10 times longer than competitor products and also doesn’t break down like other greases.
Other greases turn to oil at higher temperatures, which can then lead to bleeding into mold cavities. Syn-Lube is a full synthetic, food-grade grease that can be applied very thinly and will not break down with heat like other greases.
If you’re having issues with splay caused by bleed out in injection molding, try Syn-Lube. Applied properly, it will last longer and resist breakdown into potential bleeding.
Order or learn more about Syn-Lube.
by Nanomold Coating | May 22, 2020 | Recent Posts |
Coronavirus-related restrictions are beginning to ease up in Michigan and other states, so many sectors are getting back to work. Manufacturing is notably among them, and by extension, plastic injection molders. With employee safety top-of-mind, many plastic injection molders, whether voluntarily or by legal decree, are limiting the number of people that can be on the floor each shift. This likely means less operators working at any given time, so there’s more pressure to maximize production with the staff you do have.
Getting back up and running as quickly as possible and minimizing downtime will be crucial as plastic injection molding for manufacturing not only returns, but ramps up. Be ready and make the most of your workforce by taking this advice to speed startup and cut downtime.
Expedite Manufacturing Startup
There are many factors that could impede your ability to start up quickly, but most of them can easily be resolved.
- If your plastic injection molds are rusty due to improper shutdown, clean them with Zap-Ox™. Without scrubbing, Zap-Ox will remove rust, oxidation, build up, weld discoloration, and more.
- If a hasty shutdown has left your mold dirty, use the Nanoplas cleaner that meets your needs. All of our cleaners have a stronger spray and chemical composition, so you can clean your molds quicker without having to wipe with a rag, preventing dirt and grime from being pushed back into the metal, and saving time.
- If you over-applied a rust preventative because you didn’t know how long your molds would be in storage, or have an excessively thick application of rust preventative, start by using a Nanoplas cleaner. Going forward, use Mold Guard™, Mold Guard Green™, or Safe-T-Guard™ which are thin and truly dry rust preventatives that don’t allow corrosion to penetrate, and can be molded through at startup.
Reduce Machine Downtime
If your plastic injection molds aren’t running, that means you aren’t producing. Keep them in service and working efficiently by avoiding these common issues.
- Over-applying grease to make it through a run, because your grease is breaking down with heat. You’re likely trading one problem for another — you’re not coming up short, but you are experiencing grease bleeding into the mold cavities. Either Nanoplas grease will solve both issues. Our greases don’t break down, so there’s no bleeding. They also remain on the surface longer, extending production up to ten times longer than PTFE lubricants, so you don’t have to stop to reapply. In fact, Syn-Lube helped one manufacturer go from daily to weekly applications, and 1,000-1,500 parts per day to 24,000 parts.
- Excessive mold release build up. With efficiency being so important due to fewer operators and machine up time, making sure the molds do not have to be shut down for any reason is critical. Excessive mold release build up can lead to temporary shut down for cleaning. Nanoplas coatings and release sprays don’t build up.
If you’re experiencing any of these issues as you and your team return to work, we encourage you to give our products a try. And if you have any other problems related to plastic injection molding that aren’t noted above, don’t hesitate to contact us. We’ve likely heard it or seen it, and solved it before, and will happily do the same for you.
by Nanomold Coating | May 15, 2020 | Recent Posts |
Medical supplies. Food. Due to COVID-19, both are in extremely high demand and will be for the foreseeable future, making medical- and food-grade plastic injection molding extremely busy industries.
How busy? Back in March, Forbes reported that the Director General of the World Health Organization called on global manufacturing of medical masks, gloves and goggles to increase by 40%. Also critical, as the same article noted: nylon-plastic swabs for testing kits, plastic vials for testing kits, and ventilators. Fast forward to early May, when vaccine developments started circulating. As the New York Times noted, more than 300 million people may need a coronavirus vaccine in the United States alone, making the production of the items necessary to deliver a vaccine extremely essential.
Equally in demand is food-grade packaging. In the midst of COVID-19, it all ties back to safety. Single-serve products help minimize cross-contamination. Plastic-contained bites keep the virus on the surface of the container, minimizing the risk of coronavirus getting into the food and therefore into someone’s body. Restaurants are only open for carry-out to promote social distancing, requiring appropriate to-go containers.
All this adds up to an increased need for medical- and food-grade plastic injection molding. To step up and help meet this demand, there are three things you and your team can focus on: production efficiency, scrap reduction and startup.
Maximizing Injection Molding Production
To make your runs as productive as possible, you need to release as many products as you can while minimizing downtime. Applying a nano-thin coating when the mold is out of the press, like HCF™ Heat Cure FDA Compliant, is a good first step. It offers extraordinary release, up to 300,000 cycles, and eliminates the need for traditional mold releases that build up and require shut down for cleaning.
Minimizing Scrap
If you use a grease that doesn’t break down, you’ll significantly minimize, and possibly even eliminate, scrap from bleeding into the mold cavity, injector pins, and other areas. Applied correctly, Syn-Lube™ (high temperature, high performance, synthetic grease) and Cera-Lube™ (high performance, nano ceramic grease) mitigate bleed off. Both remain on the surface longer than PTFE lubricants, extending production time up to ten times longer. In fact, Syn-Lube helped one manufacturer go from 1,000-1,500 parts per day, to 24,000 parts, with the product lasting weekly versus daily.
Speedier Startup
When it comes time to store your molds, use a dry rust preventative, like Safe T Guard™. Unlike other rust preventatives that claim to be dry, Safe T Guard truly is, so it won’t break down grease and can be molded through at startup, getting your production up and running faster and reducing scrap significantly.
If the onset of COVID-19 and related quarantine orders didn’t give you time to properly store and maintain your molds, a cleaner like Zap-Ox™ will have them back in operating form ASAP. Zap-Ox cleans gassing and burn marks, buildup, and more with little-to-no scrubbing, saving maintenance and downtime.
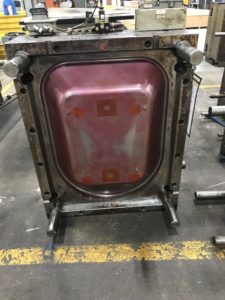
Before using Nanoplas Zap Ox
Note that all Nanoplas products mentioned above are FDA-compliant or NSF-registered, making them appropriate for medical and food-grade plastic molding.
Whether you increase production by focusing on one, two, or all three of the areas discussed, or are trying to maintain the same output with less staff due to health and safety measures, we here at Nanoplas want to help, so don’t hesitate to contact us. We’re happy to provide a free sample, product recommendation, or answers to any questions you might have.
by Nanomold Coating | Apr 30, 2020 | Recent Posts |
This year’s plastic injection molding trends look to continue several of the big initiatives from 2019 in some exciting ways. As companies consistently strive to improve in all aspects of their businesses, increased efficiency and reduced downtime remain two of the most important benefits.
Moving into 2020, we see a lot of improved technology, software and even thought processes that will help companies achieve their goals. Here are five plastic injection molding trends to look for in 2020:
1. Bio-Plastics and Environmentally Friendly Additives
Companies in every industry—but particularly plastics—are always trying to reduce the environmental impact of products and operations. This year, we expect to see a lot more bio-resins made from renewable resources (plant and vegetable extracts like corn or sugarcane) that are far safer for disposal and also more energy-efficiency in manufacturing.
Much of this trend is being driven by packaging. As companies look to reduce their environmental footprints, they’re seeking better packaging solutions, which is helping drive the increase in bio-resin use.
In a related trend, we’re seeing a push toward making conventional thermoplastics biodegradable. Adding metal compounds to the plastic leads to oxidation, breaking down the plastic and allowing microorganisms to do the rest. Environmentally friendly additives to traditional plastics along with bio-plastics are going to have an impact on the industry as a whole and, of course, on the environment.
2. Automation
When we talk about the automation and plastic injection molding trends for 2020, we’re specifically referencing software. Improved software and technology, which will only continue to advance, will allow manufacturers to save time, reduce waste and increase throughput.
Being able to analyze designs and plastic flow through molds will mean parts can get into production quicker as the time required for the testing and refinement phases is drastically cut.
Programming is being simplified, maintenance is becoming more efficient, cycles are getting faster and downtime is being significantly reduced. With better, more thorough control of the entire process, software automation is going to improve production throughout the industry.
3. Reinforced Plastic Materials
One of the big trends in 2019 is going to continue through 2020 and beyond as the automotive and aerospace industries seek the just-as-strong-but-not-as-expensive solutions that are also gaining traction in the medical industry and with the military due to the proven durability of the materials.
Plastics reinforced with metal, glass, carbon and graphite substitute for what used to be metal parts. The weight of the reinforced plastics is similar if not less, there is no decline in strength or function, and the cost savings can be huge.
4. Lightweight Materials
As reinforced plastics are already replacing exotic materials with parts that are of comparable or lighter weight, there’s an increased demand in less weight in general. In cars, particularly electric and hybrid models, less weight means better gas mileage or longer battery life, so developing lightweight injection molding products continues to be in high demand.
In other industries, the benefits may be less obvious but are still notable. Lightweight medical uses like joint replacements and stents will dramatically benefit patients, but even the improvements in tools and equipment can increase the efficiency (and costs) in healthcare
5. Sustainability
In any type of manufacturing, sustainability remains important and efforts to improve persist. In injection molding, in addition to bio-resins and eco-friendly additives, efforts will continue to reduce waste and enhance recycling.
We’re going to see a larger focus on using as many recyclable materials as possible—likely with goals of 100%—throughout the injection molding industry. Since plastics have always been under additional scrutiny, we can expect even more motivation from manufacturers looking to improve their environmental footprints.
Nanoplas products are designed to reduce your costs through cutting downtime and increasing efficiency. With many of the latest plastic injection molding trends based on precisely those goals, our products will help you further embrace whichever trends you choose to focus on this year and beyond.
by Nanomold Coating | Mar 16, 2020 | Manufacturing, Plastics |
Coronavirus: Will the Molding Industry Be Impacted?
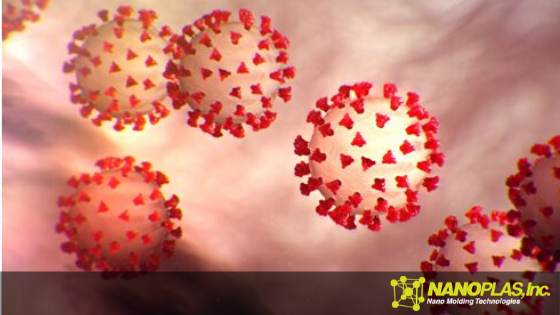
Most likely, the answer is yes. Wuhan and other parts of China shut not only their manufacturing down, but entire cities. That effect has rippled, as COVID-19 has spread and continues to spread, growing to become the global health pandemic that it is today.
Exactly how the coronavirus will hit the molding industry is to be seen, but we can make some educated guesses based on what’s already happening. Here are our five predictions and expectations, plus advice on how to deal with a few of them.
Supply Chain Squeeze
Due to manufacturers in China and elsewhere closing or scaling back operations, supply chains are going to cut down to a trickle or temporarily dry up completely. While you and your customers might have a stockpile of raw material, it may not be enough to last until normal operations return. The good news is that normal operations are starting to resume, so supply chain issues are likely to be temporary.
Shipping Delays
Fact: China has seven of the world’s top 10 busiest ports. With all of the travel restrictions in China, a majority of port workers and laborers couldn’t get to their jobs. With little to no one to do the work, the shipping slowed to a halt, causing a hit to the industry. What does this mean for you? Don’t expect on-time deliveries, as supplies and components are likely to be bottlenecked and delayed. That being said, you likely won’t be the only one experiencing this pain point, so do your best to keep your patience and navigate the situation with grace.
Trade Shows Postponed or Canceled
Per medical experts, people should avoid large gatherings, as the coronavirus is most commonly spread through contact with an infected individual and symptoms can take up to 14 days to show up. Many trade shows are heeding this advice and either canceling or postponing their events. While these changes are an inconvenience at best, they are doing their part for the industry and their communities to help curb the spread of this infectious disease, and that’s something we should all appreciate.
Labor Issues
As more and more cases of coronavirus are diagnosed here in the U.S., it’s likely your employees will be impacted. Whether it’s school closures, like we’ve experienced here in Michigan (all K-12 schools are closed through April 5, 2020, per Governor Whitmer’s order), they have a sick family member, or suspect they’re symptomatic, you may experience a shortage of labor. Do your best to empathize, as this is also stressful for them. Be flexible with your sick and personal time off policies where you can. Also, check-in often, ask for open and honest input and feedback, and communicate frequently. This will make great strides in reassuring your workforce and boosting morale.
Economic Downturn
There’s already talk amongst the media that we’re tipping into a recession. While financial experts agree that a recession is a probability, if it does happen, they also say it’s unlikely to be as bad or as long lasting as the Great Recession that began in 2007. Generally, with recession comes increased pricing, decreased spending and other economic downturns, but it’s to be determined if and how long we’ll have to bear these hardships.
As you navigate the coronavirus and its impacts on your business, remember: we’re all in this together and we all have an important part to play. How you choose to play it is up to you, but we hope you take the high road, whatever that may be.