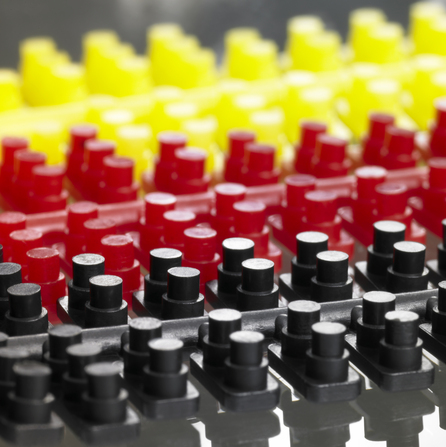
On the tooling side, I have seen many times when shut-off draft angles contribute to flash. Typically, it’s from wear with the shut-off angle being too close to vertical. It is best to keep your shut-off angles 5 degrees or greater but at times the part design does not allow this. If this is the case, parting line locks or lock angles become a necessity. The leader pins and bushing cannot be relied on to protect the shut-offs. I personally am a fan of the zero draft side locks. In any case, the draft angle of the lock angle or parting line lock needs to be less than the draft of the shut-off to be able to protect it from wear.
It is also critical, especially on large tools that the water temps are the same on both the cavity and core to protect the shut-offs. Thermal-expansion from running the two halves at different temperatures can contribute to wearing out the shut-offs and causing flash. I know there are many times where water temperatures are used on one half to address part quality issues or sticking issues, but I wanted to bring up the disadvantage with the shut-offs possibly being an issue.
I also want to bring up how improperly spotting the tool during the build process can contribute to wear issues causing flash. Every tool maker has their own interpretation of how to spot a tool. Tool makers, do not take this personal, I’ve been hands on for 26 years and in dealing with the maintenance side of tooling the past 12 + years I’ve found this to be an issue at times. If the shut-offs are spotted where they are hitting too hard on low draft shut-off angles you are at high risk for wear or galling. Even on the repair side when spotting down weld, the weld should not hit harder than the existing parting lines.
Another area that can contribute to flash is with inadequate parting line maintenance. The parting lines should be maintained so they stay clean and free from build and debris. Also, flaking from sub gates, cashew gates and runner system and pins can cause parting line damage contributing to flash. Any issues with flaking should be addressed and eliminated. This is a subject I will address in detail down the road along with why runner boss pins are acceptable to flash.
The machine can also contribute to flash issues. If the platens are not clamping up parallel to each other you will have uneven clamp force transmitted to the mold. To diagnose the mold could be rotated 180 degrees to see if the flash changes. If this is a concern the tie bars should be checked with a strain gauge to verify they have equal strain. The machine should also be checked for level during this procedure.
The size of the mold relative to the platen surface area can also contribute to flash issues. When running an undersized mold in a press, you can cause platen distortion leading to uneven clamp force to the mold. Note that flash from this root cause will typically show up near the center of the mold where the platen distortion is at the maximum. Another similar issue is with any tool that has an offset sprue or hot runner and the tool being mounted off center of the platen. The flash in this case will typically be the area located farthest from the center of the platen. A solution to both of these issues is to add support by adding stand-off rails to the mold that equal the stack height of the mold. Or, extending the clamp plates out and adding support pillars outside of the mold.
At times the machine itself is not obtaining the desired clamp force. If there is a hydraulic leak, a press can have issues where it may not achieve desired clamp force, or after reaching the desired clamp force the leakage can cause the clamp force to be reduced. Also, verify the machine doesn’t have a setting that allows the clamp pressure to drop early in the cycle or start filling during tonnage build. Machines can also decompress the clamp at the end of pack/hold to allow for a quicker clamp opening.
Dial indicators and other devices can be used to help diagnose if the clamp is blowing open. If you are detecting clamp movement this will help focus the troubleshooting to the machine rather than blaming the mold.
The ideal situation is to have uniform clamp force over the entire surface of the mold to overcome the cavity pressure developed during processing, having a tool that is robust enough to prevent deflection and design to reduce wear issues. Going back to part 1 of this series and the 3 criteria for flash free molding, the concept is “you can’t get something through nothing”.
I hope you found this series beneficial in understanding flash and root causes. I could have gone much deeper on this topic on flash with venting, hydraulics, components and runner pins, but these all will be addressed in the future with related topics. If you have further questions on this subject or any other subject, please feel free to contact me through the blog. I will do my best to get back to you promptly.