by Admin | Nov 13, 2019 | Recent Posts |
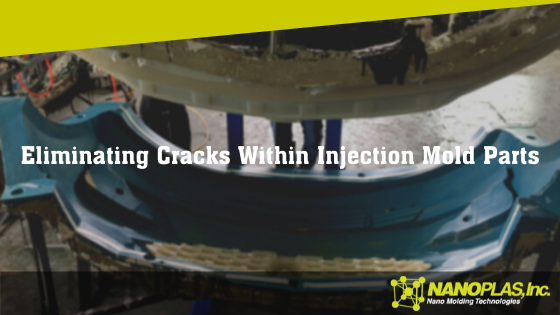
What Is Cracking in Injection Molding?
When a part is physically fractured or broken, you’re experiencing cracking. Cracks usually occur due to post-molding conditions, but when troubleshooting cracking, you want to know exactly when the cracking is happening as it will help you efficiently address potential issues and ultimately solve the problem.
Troubleshooting Cracks
In addition to post-molding conditions, cracking can be caused by a number of process settings, including second-stage pressure, melt temperature, residence time in barrel, ejection, part removal, operator error, mold breakaway and gate seal.
Molding Process | Mold | Machine | Material |
High second-stage pressure | Undercuts | Overheating | Moisture content |
Melt temperature | Sharp corners | Lack of process control | Contamination |
Residence time in barrel | Lack of draft | Regrind |
Ejection | Lifter or slide corners |
Part removal |
Operator |
Mold breakaway speed |
Gate seal |
Table 24.1 Cracking Troubleshooting Chart, found in Injection Molding Advanced Troubleshooting Guide: The 4M Approach (p. 224)
How to Eliminate Cracking in Injection Molding
While cracks often occur post-mold, identifying the underlying issue is extremely important in being able to prevent cracking from happening. Check the part design—are there areas with sharp corners that act as stress risers and initiate cracks? If so, adding more radius to those areas can alleviate the stress and thus the cracks.
During the molding process, you could be facing high second-stage pressure, causing the material to stick which can lead to cracks when the mold opens or during ejection. A high melt temperature or improper residence time in the barrel could degrade the part and make it susceptible for cracking during ejection.
Since cracking usually occurs during ejection, it’s important to determine if the ejection itself is causing the issue or if it’s another issue that leaves the part vulnerable to ejection. Stop the mold process prior to ejection and look for cracks. If you see them, you know you have another issue. If there are no cracks, eject the part and check again. If you see cracks this time, you know there’s an ejection issue.
Nanoplas mold-release sprays are invaluable when it comes to ejecting parts and can be a tremendous help if you’re experiencing cracking.
If the part shows no cracks after ejection, it could be a part-removal issue or even an operator error. Something as simple as an operator handling the part could lead to cracking, which generally means there’s a design flaw that needs to be addressed. Simple handling of a part shouldn’t lead to cracking.
Cracking is a troublesome issue, but it can give you a lot of necessary information as to what needs to be improved to eradicate the problem.
Want to learn more? Check out these other great articles that solve common injection mold issues:
Source: Injection Molding Advanced Troubleshooting Guide: The 4M Approach by Randy Kerkstra and Steve Brammer.
by Admin | Nov 13, 2019 | Plastics |
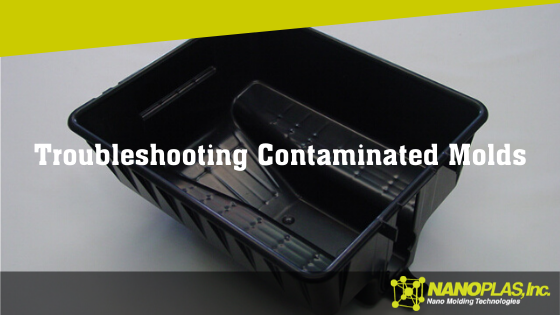
What Is Contamination in Injection Molding?
Contamination appears as discoloration, streaks, splay, delamination and other types of defects. Because it’s such a broad area with multiple possible culprits, is best to start with the usual suspect: the material brought to the molding machine.
Troubleshooting Contamination
Starting with the material, then working backward from there if necessary, you’re more likely to catch the root cause of the contamination earlier in the process, saving you time and energy and getting things back up and running as soon as you can.
Molding Process | Mold | Machine | Material |
Poor changeover | Hot runner hang-up | Hang-up areas | Improper storage |
High melt temperature | High hot runner temperature | Anti-seize | Regrind |
| Wear Surfaces | Robot contamination | Incoming contamination |
| Lubricants | | Mixed Materials |
| Cleaning | | |
How to Eliminate Contamination in Injection Molding
Start with material storage. If your material is left in an open container, it’s nearly certain you’ll end up with a contaminant. Every molding shop has dust, dirt, cardboard, wood, metal, grease and other potential contaminants in abundance. If your materials aren’t stored properly, any one of those foreign substances can lead to contamination and a rejected part.
Another potential issue with the material is regrind. Make sure no one is grinding the wrong material with other materials (for example, just because one material is the same color as another doesn’t mean it’s the same material). Improper storage of regrind can be an issue if foreign substances can sully the material. The machine itself, if not properly cleaned, can add contaminants to the regrind.
Avoid mixing materials. Not only can putting the wrong materials together lead to contamination, but some—like PVC and acetal—are dangerous when mixed.
If you confirm everything is being done right with your materials, you can move into the process settings, mold and machine to see if any contaminants are being introduced there.
Want to learn more? Check out these other great articles that solve common injection mold issues:
Source: Injection Molding Advanced Troubleshooting Guide: The 4M Approach by Randy Kerkstra and Steve Brammer.
by Admin | Sep 30, 2019 | Plastics |
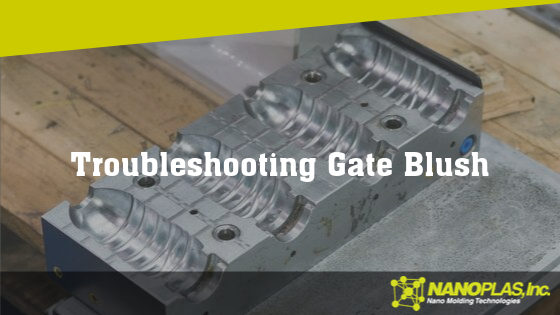
When you see a non-uniform fanning out from the gate, which appears as a different color or gloss level to the surrounding plastic, you may be dealing with gate blush.
What is Gate Blush?
Also known simply as blush, or gate shear or halos, gate blush is a dull or discolored portion usually found just inside the gate location of a part. Occasionally, gate blush will show up in areas where there’s a wall-stock transition.
Blush can be confused with jetting, flow lines and flow marks, so you need to be careful when troubleshooting. Since jetting gives a blush-like appearance, you’ll want to confirm you’re dealing with gate blush before troubleshooting.
Troubleshooting Gate Blush
If you’re experiencing blush, it could be due to the molding process, mold itself or the machine. See below for possible causes.
Molding Process | Mold | Machine | Material |
Injection velocity | Gate geometry | Nozzle | |
Nozzle temperature | Hot runner tip temperature | Machine performance | |
Mold temperature | Cold slug well | | |
Melt temperature | Gate location | | |
Table 18.1 Gate Blush Troubleshooting Chart, found in Injection Molding Advanced Troubleshooting Guide: The 4M Approach (p. 142)
How to Eliminate Gate Blush in Injection Molding
Most often, the culprit is an injection velocity that’s set too high. However, the solution isn’t as simple as lowering the injection velocity. Not at first, anyway. Before you reduce the fill speed, ensure your gate size and design are adequate. If your blush is caused by something with the tooling design and you try to process around it, you risk other defects, particularly short shots.
Pay attention to all temperatures: nozzle, mold and melt. If the nozzle or mold temperatures are too high, it can impact the first plastic in the mold, resulting in blush. A melt temperature that’s too high can hurt the quality of the initial formation of plastic out of the gate.
As we mentioned, check the size and design of the gate before attempting to process around a potential tooling issue. If the gate isn’t flush to the mold surface, that needs to be adjusted before you change any of the settings with the molding process.
If the problem is with the machine itself, your first place to look should be the nozzle. Its length, style, tip type, tip orifice and heaters all need to match the documented process.
Although less common, there could be issues with the material. PC/ABS blends and TPOs tend to be the most prone to gate blush.
Want to learn more? Check out these other great articles that solve common injection mold issues:
Source: Injection Molding Advanced Troubleshooting Guide: The 4M Approach by Randy Kerkstra and Steve Brammer.
by Admin | Aug 26, 2019 | Plastics |
Are you experiencing bubbles during your injection molding processes? Let’s go through the possible causes—and fixes—to get rid of bubbles.
What are Bubbles in Injection Molding?
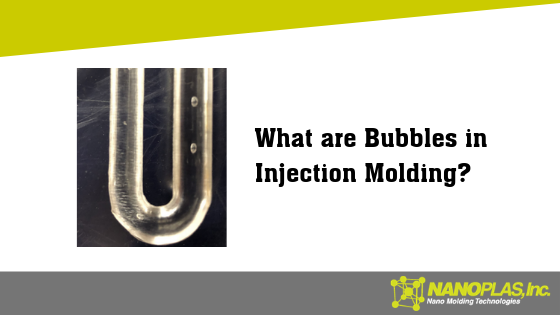
Bubbles, sometimes known as gas traps or blisters, are cosmetic defects that detract from the looks of the part, which is especially irritating if the part will be seen. When diagnosing bubbles, you need to be careful, as the characteristics are similar to voids. Before you can troubleshoot bubbles (or voids), you need to be sure which one you’re dealing with.
Is it a Bubble or a Void?
When gas forms in the melt stream, you end up with bubbles. Voids are instances of plastic shrink that creates a vacuum in the plastic wall stock.
To determine whether you’re looking at bubbles or voids, slowly heat the area with a torch or heat gun. If it’s a void, the wall stock will collapse and show a sink. If it’s a bubble, the wall stock will swell due to the gas inside expanding.
Troubleshooting Bubbles
Once you know you’re dealing with bubbles, here are the possible causes:
Molding Process | Mold | Machine | Material |
High melt temperature | venting | Machine performance | Moisture content |
Low back pressure | Hot runner temperatures | Crack in feed throat leaking water | Transparent materials |
High decompression | Cracked water line | Screw design | contamination |
| Venturi effect | | unmelts |
Table 18.1 Bubbles Troubleshooting Chart, found in Injection Molding Advanced Troubleshooting Guide: The 4M Approach (p. 166)
How to Eliminate Bubbles in Injection Molding
Try running a series of short shots as your first troubleshooting step. Doing so will help you see where the bubble begins to appear, and if it only shows up in specific locations, you can often determine the root cause.
More often than not, the cause of bubbles is excess gas in the part, which can come from high melt temperature, low back pressure or high decompression. Adjusting these settings, again using short shots if you can, could solve the problem.
Otherwise, you’ll need to run through the checklist in the table above and adjust settings as necessary.
As always, using Nanoplas’ innovative line of injection mold coatings such as Heat Cure and Quick Cure, or sprays like Tuff Kote and Dri Kote, will help avoid injection molding problems, particularly when the cause is with the mold, material or machine.
Want to learn more? Check out these other great articles that solve common injection mold issues:
Source: Injection Molding Advanced Troubleshooting Guide: The 4M Approach by Randy Kerkstra and Steve Brammer.
by Admin | Jul 22, 2019 | Plastics |
What Causes Plastic Delamination in Injection Molding?
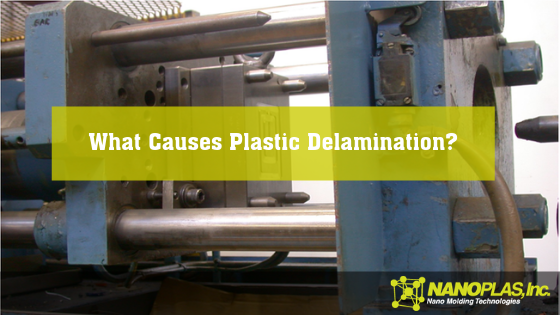
When you’re able to peel the surface of a molded part, layer by layer, you’re dealing with delamination, an injection-molding defect that is sometimes also known as lamination or layering. This is a bad sign—delamination hurts the strength of the part, thus making it unreliable and potentially dangerous, depending on the part’s intended use.
Common Causes of Delamination
Just like most injection-molding defects, delamination can be caused by one or more of several potential issues. The most common: incompatible materials. When two materials can’t bond together, it results in separation that very quickly becomes delamination.
“Incompatible materials” can be a number of things.
Two plastics that can’t properly bond.
Excess release agents coating the mold, which is why it’s so important to properly apply release agents.
Too much moisture on the material, which is usually due to a failure to completely dry the material before using it. During the molding process, moisture becomes steam, which leads to surface delamination.
Delamination can also be caused by high shear stress, too much injection speed, a high melt temperature or material degradation, so you should look at all potential issues while troubleshooting even though you’ll most frequently find your issue with the incompatibility of materials.
How to Eliminate Plastic Delamination
Preventing delamination first requires you to know the cause, but once you do, you should be able to get rid of the problem.
Make sure you’re using plastics that will properly bond with each other. Always take extra care to ensure every part that goes into the mold has been completely dried. When applying mold-release sprays, do so as intended so as not to overspray. If you find that you need more release spray than you know is wise, then your issue could be with the mold itself and you may want to rethink the design to make ejection easier.
If you find the issue to be with the molding process, such as shear stress or melt temperature, adjust those settings as necessary to eliminate delamination.
Nanoplas Mold Release Products
Our Heat Cure™ and Quick Cure coatings are specifically designed to allow non-stick ejection and prevent delamination. They are semi-permanent coatings applied in-house and can last for thousands of shots.
As opposed to other sprays that go on heavy and can cause buildup in the mold, our Tuff Kote and Dri Kote high-performance sprays go on light and are ideal for avoiding delamination.
Remember: with all mold-release products, make sure you’re applying them properly.
Contact us to get a free sample of our Nanoplas mold-release sprays.