by Admin | Jun 30, 2020 | Manufacturing, Plastics, Recent Posts |
Advantages of Mold Maintenance
Injection molders around the world are striving to make their operations more efficient, and more productive. One area that is often overlooked when it comes to gaining such advantages is mold maintenance.
A well-defined and consistent mold maintenance program helps improve efficiency by ensuring the molds are ready for production when needed. A Nanoplas cleaner, when used with a rust preventative, and a grease that does not break down not only cleans the mold, but also prepares it for the next run.
While applying the cleaner, rust preventative, and grease, take the time to thoroughly inspect the mold. Doing so will give you the chance to identify problems or wear on the mold before they become significant issues. As part of your maintenance log, make a note of any concerns, address the ones you can, and track the progression of any issues you can’t fix.
When it comes time to get the mold back into production, products used to clean and prepare the mold should not be a problem or cause a delay. The Nanoplas line of products are formulated to mitigate this issue. They do not cause bleeding or startup scrap, so you can mold right through them and save time getting the production run moving.
Integrating a maintenance program as a core element into your production strategy may allow you to realize significant gains in productivity by reducing startup issues and downtime, making your operation more efficient and profitable. To learn more about how the Nanoplas family of products can play a role in that strategy, contact us today.
by Nanomold Coating | Mar 16, 2020 | Manufacturing, Plastics |
Coronavirus: Will the Molding Industry Be Impacted?
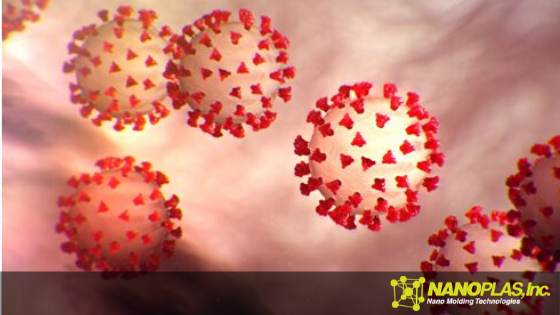
Most likely, the answer is yes. Wuhan and other parts of China shut not only their manufacturing down, but entire cities. That effect has rippled, as COVID-19 has spread and continues to spread, growing to become the global health pandemic that it is today.
Exactly how the coronavirus will hit the molding industry is to be seen, but we can make some educated guesses based on what’s already happening. Here are our five predictions and expectations, plus advice on how to deal with a few of them.
Supply Chain Squeeze
Due to manufacturers in China and elsewhere closing or scaling back operations, supply chains are going to cut down to a trickle or temporarily dry up completely. While you and your customers might have a stockpile of raw material, it may not be enough to last until normal operations return. The good news is that normal operations are starting to resume, so supply chain issues are likely to be temporary.
Shipping Delays
Fact: China has seven of the world’s top 10 busiest ports. With all of the travel restrictions in China, a majority of port workers and laborers couldn’t get to their jobs. With little to no one to do the work, the shipping slowed to a halt, causing a hit to the industry. What does this mean for you? Don’t expect on-time deliveries, as supplies and components are likely to be bottlenecked and delayed. That being said, you likely won’t be the only one experiencing this pain point, so do your best to keep your patience and navigate the situation with grace.
Trade Shows Postponed or Canceled
Per medical experts, people should avoid large gatherings, as the coronavirus is most commonly spread through contact with an infected individual and symptoms can take up to 14 days to show up. Many trade shows are heeding this advice and either canceling or postponing their events. While these changes are an inconvenience at best, they are doing their part for the industry and their communities to help curb the spread of this infectious disease, and that’s something we should all appreciate.
Labor Issues
As more and more cases of coronavirus are diagnosed here in the U.S., it’s likely your employees will be impacted. Whether it’s school closures, like we’ve experienced here in Michigan (all K-12 schools are closed through April 5, 2020, per Governor Whitmer’s order), they have a sick family member, or suspect they’re symptomatic, you may experience a shortage of labor. Do your best to empathize, as this is also stressful for them. Be flexible with your sick and personal time off policies where you can. Also, check-in often, ask for open and honest input and feedback, and communicate frequently. This will make great strides in reassuring your workforce and boosting morale.
Economic Downturn
There’s already talk amongst the media that we’re tipping into a recession. While financial experts agree that a recession is a probability, if it does happen, they also say it’s unlikely to be as bad or as long lasting as the Great Recession that began in 2007. Generally, with recession comes increased pricing, decreased spending and other economic downturns, but it’s to be determined if and how long we’ll have to bear these hardships.
As you navigate the coronavirus and its impacts on your business, remember: we’re all in this together and we all have an important part to play. How you choose to play it is up to you, but we hope you take the high road, whatever that may be.
by Admin | Feb 21, 2016 | Manufacturing, Plastics, Recent Posts |
The infographic below is from our friends at Economy Glass in Australia. It does a nice job of explaining nano coatings, and their impact on manufacturing.
Check it out:

by Admin | Aug 26, 2015 | Manufacturing, Recent Posts |
Quality. This one word sums up the need for having a defined mold maintenance program. Quality parts come from quality molds. But just like anything that is used as a tool, wear and degradation are part of the process. Having a maintenance program is an investment in quality.
There are a few simple things that can make a significant difference, and are part of any program. The most basic is a maintenance log of your molds. This allows you to document little things that come up, as well having some level of documentation and information should something larger present itself with the mold. The other is to perform periodic maintenance as the tools are run in production.
Keeping track of the materials used for mold maintenance such as what type of degreasers and cleaners are used, what rust preventatives are applied, and what types of greases are being used can also help you identify opportunities for improvement at start up or when preparing the mold for storage.
There are also four factors that can determine the frequency and extent of maintenance required.
Mold Materials: The amount of wear on a mold, and the speed at which the mold wears will be directly related to the softness of the materials used to make it. Softer molds, like those made from aluminum and other conventional mold materials will wear faster than hardened steel.
Environment and Use: There are many factors under this category that can be monitored as part of your program. Monitoring and documenting factors such as clamp pressure and injection pressure can help to avoid subjecting the tool to excessive or extreme conditions. Lubrication of the appropriate and required components can also help with the overall longevity of the mold, and can be a factor in determining the optimal maintenance schedules. Finally, the way the mold is opened and closed can also be a factor in the overall maintenance requirements.
Molding Materials: There are two factors when it comes to what is being shot into the mold that can have a major impact. The first is melt temperature. Higher melt temperature materials will cause a mold to wear faster as it exposes the metals or material of the mold more heat exposure. The second is the type of fill materials used in the molding materials. In most cases, the materials are not liquid, and act as abrasives. Materials such as fiberglass, Mica and even wood are very abrasive.
Mold Complexity: Complex tooling, making complex parts will require a higher level of maintenance than a simple two plate, low precision part mold. Ejectors, slides, lifters, hot runners and small or thin mold components and others add to the maintenance that will be required for a tool.
Mold maintenance can play a significant role in helping to maintain consistent, high quality parts. By following the basic practices of maintaining a mold maintenance log and performing periodic maintenance, as well as taking into account the four factors that impact the frequency and extent of maintenance required, your quest for quality can be realized.
To learn more about how that Nanoplas family of mold maintenance products can be part of your successful program, contact us today!
by Admin | Aug 12, 2015 | Manufacturing, Plastics, Recent Posts |
One of the challenges for injection molders is efficiency. The cycle times for plastic parts can range from 30 seconds to more than a minute. One of the primary contributors to that time and one of the longstanding constraints is cooling time. It is always a trade off of waiting for the parts to properly cool to avoid warping and shrinking, and maximizing productivity.
The concept of additive manufacturing or what used to be considered or associated with laser sintering, is a way to potentially improve the productivity and efficiency of your mold by taking advantage of conformal cooling.
The additive manufacturing process allows the toolmaker to lay down one layer of the mold at a time, creating the ability to get away from straight line drilling of cooling channels that are not as efficient. By utilizing conformal cooling channels that conform or run closer to the shape of the part allows for more efficient cooling process, and has led manufacturers to realize reduced cycle times by as much as 25-40%!
The creation of conformal cooling channels is something that must be considered when designing the tool, and is often considered an optimization task. In many of the mold software tools, are able to simulate the conformal channels, and their impact on the tool.
Making your operation more efficient is not easy. Additive manufacturing concepts for tool creation is one concept that can potentially have a very positive impact.
The Nanoplas line of mold maintenance products, and our mold coatings can also have a significant impact on your productivity levels. Contact us today to learn more about how our products can help you achieve your goals!
by Admin | Aug 5, 2015 | Manufacturing, Recent Posts |
In today’s ever-increasing competitive environment, the ability to produce parts profitably is harder and harder. One of the areas that many molders have looked towards to save time and costs is the concept of Rapid Injection Molding. One area that can make this idea even more feasible is through a progressive mold maintenance program.
Rapid Injection Molding, or RIM, is a way to get parts made faster through the use of molds that are easier and faster to produce. With the molds designed for lower volume production runs, how they are maintained can be the difference between having to produce a new mold, and maximizing the production value of the existing mold. As many of the molds are made from aluminum, it is critical that they be cleaned well after each run.
The cleaning products used in injection molding have gone through major changes of late. Products like Mold Brite and Zap-Ox from Nanoplas are specially formulated to effectively clean molds of various materials, and are very effective for maintaining RIM molds.
Another product that can have a significant impact on mold life is the lubricating grease used. The Nanoplas Cera-Lube Nano Ceramic Grease is a high performance lubricant that works very well and can help prolong your RIM tooling.
Finally, based on the lower volumes, an area that can make RIM tooling even more effective is mold release. There has been a lot of progress in the formulations in this area as well. The challenge with RIM is that downtime to apply mold coatings can be too long. Nanoplas now has a mold release spray called Dri-Kote that is quick drying and with good bonding to metal molds.
Getting the maximum value from your RIM tooling is critical, and the way the mold is maintained and treated can make the difference. Many shops have been using the same maintenance products for a very long time, however there are alternatives that can make a difference in your workflow and tooling.
We invite you to check out the Nanoplas family of products and let us show you how they can make a difference in your shop.