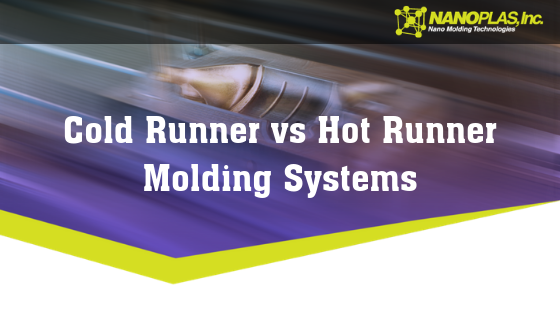
Cold Runner Vs. Hot Runner Molding Systems
Cold Runner Vs. Hot Runner Molding Systems
Why should you choose a hot-runner mold system over a cold-runner mold system (or vice versa)? Each type of molding system has unique features that help determine exactly which one is best for you.
Cold-Runner Mold Systems
Called a cold-runner mold system because the runners are the same temperature as the molds, there are two types of cold-runner systems: a three-plate system and a two-plate system.
Three-plate systems allow the part to be ejected from the runner without an ejection system, but are a little more complicated than a two-plate system, which does require an ejection system to remove the part and the runner from the mold. Two-plate systems can handle most molds, however a three-plate system is friendlier when it comes to complex designs.
In a cold-runner mold system, the runner has to be larger than the part. Otherwise, you run the risk of underfilling the mold. One big advantage over a hot-runner system is the ability to use more types of polymers without concern for heat sensitivity.
Cold runners are less expensive than hot runners and are easily maintained as well, but they can create waste unless you can recycle or melt down the extra material.
Pros and Cons of Cold Runner System
Pros
- Inexpensive
- Few restrictions on types of polymers
- Easy to maintain
- Easy to change colors
Cons
- Runners have to be removed
- Takes longer than a hot-runner system
- Creates waste >> read more on reducing injection mold waste and scrap.
Hot-Runner Mold Systems
There are two types of hot-runner mold systems, both of which use two plates heated by a manifold system. Externally heated molds allow you to use more heat-sensitive polymers while internally heated molds generate better flow control. Depending on your materials and applications, you may prefer (or need) one type over the other.
Hot runners are more expensive than cold runners (in initial investment and maintenance), but they can handle higher volumes and larger parts and also don’t generate any waste. In some cases, the lack of waste balances with the higher maintenance cost to actually be about the same net cost as a cold-runner system.
Overall, hot-runner molds produce parts with more consistent quality and do so with faster cycle times, but it’s not as easy to change colors nor can hot runners accommodate some heat-sensitive polymers.
Pros and Cons of Hot Runner System
Pros
- Fast cycle time
- Consistent quality
- Very little waste
- Ideal for larger parts and higher volumes
Cons
- Expensive to purchase and maintain
- Not ideal for some heat-sensitive polymers
- Difficult to make color changes
Which System is Right for You?
Depending on exactly what you’re doing with your molds—materials, applications, size, volume, etc.—you may have a clear answer as to the best mold system or it may be more complicated. For instance, if you’re only working with heat-sensitive polymers, a cold-runner mold system is probably your best choice. If you’re producing large volumes and need faster cycle times, you’re probably looking for a hot-runner mold system.
However, those aren’t definite answers and shouldn’t be taken as such. You need to consider every facet of what you’re doing to determine the best system for you. Feel free to contact us if you’d like to talk about which type of mold system is your best option.