by Admin | Aug 26, 2015 | Manufacturing, Recent Posts |
Quality. This one word sums up the need for having a defined mold maintenance program. Quality parts come from quality molds. But just like anything that is used as a tool, wear and degradation are part of the process. Having a maintenance program is an investment in quality.
There are a few simple things that can make a significant difference, and are part of any program. The most basic is a maintenance log of your molds. This allows you to document little things that come up, as well having some level of documentation and information should something larger present itself with the mold. The other is to perform periodic maintenance as the tools are run in production.
Keeping track of the materials used for mold maintenance such as what type of degreasers and cleaners are used, what rust preventatives are applied, and what types of greases are being used can also help you identify opportunities for improvement at start up or when preparing the mold for storage.
There are also four factors that can determine the frequency and extent of maintenance required.
Mold Materials: The amount of wear on a mold, and the speed at which the mold wears will be directly related to the softness of the materials used to make it. Softer molds, like those made from aluminum and other conventional mold materials will wear faster than hardened steel.
Environment and Use: There are many factors under this category that can be monitored as part of your program. Monitoring and documenting factors such as clamp pressure and injection pressure can help to avoid subjecting the tool to excessive or extreme conditions. Lubrication of the appropriate and required components can also help with the overall longevity of the mold, and can be a factor in determining the optimal maintenance schedules. Finally, the way the mold is opened and closed can also be a factor in the overall maintenance requirements.
Molding Materials: There are two factors when it comes to what is being shot into the mold that can have a major impact. The first is melt temperature. Higher melt temperature materials will cause a mold to wear faster as it exposes the metals or material of the mold more heat exposure. The second is the type of fill materials used in the molding materials. In most cases, the materials are not liquid, and act as abrasives. Materials such as fiberglass, Mica and even wood are very abrasive.
Mold Complexity: Complex tooling, making complex parts will require a higher level of maintenance than a simple two plate, low precision part mold. Ejectors, slides, lifters, hot runners and small or thin mold components and others add to the maintenance that will be required for a tool.
Mold maintenance can play a significant role in helping to maintain consistent, high quality parts. By following the basic practices of maintaining a mold maintenance log and performing periodic maintenance, as well as taking into account the four factors that impact the frequency and extent of maintenance required, your quest for quality can be realized.
To learn more about how that Nanoplas family of mold maintenance products can be part of your successful program, contact us today!
by Admin | Aug 12, 2015 | Manufacturing, Plastics, Recent Posts |
One of the challenges for injection molders is efficiency. The cycle times for plastic parts can range from 30 seconds to more than a minute. One of the primary contributors to that time and one of the longstanding constraints is cooling time. It is always a trade off of waiting for the parts to properly cool to avoid warping and shrinking, and maximizing productivity.
The concept of additive manufacturing or what used to be considered or associated with laser sintering, is a way to potentially improve the productivity and efficiency of your mold by taking advantage of conformal cooling.
The additive manufacturing process allows the toolmaker to lay down one layer of the mold at a time, creating the ability to get away from straight line drilling of cooling channels that are not as efficient. By utilizing conformal cooling channels that conform or run closer to the shape of the part allows for more efficient cooling process, and has led manufacturers to realize reduced cycle times by as much as 25-40%!
The creation of conformal cooling channels is something that must be considered when designing the tool, and is often considered an optimization task. In many of the mold software tools, are able to simulate the conformal channels, and their impact on the tool.
Making your operation more efficient is not easy. Additive manufacturing concepts for tool creation is one concept that can potentially have a very positive impact.
The Nanoplas line of mold maintenance products, and our mold coatings can also have a significant impact on your productivity levels. Contact us today to learn more about how our products can help you achieve your goals!
by Admin | Aug 5, 2015 | Manufacturing, Recent Posts |
In today’s ever-increasing competitive environment, the ability to produce parts profitably is harder and harder. One of the areas that many molders have looked towards to save time and costs is the concept of Rapid Injection Molding. One area that can make this idea even more feasible is through a progressive mold maintenance program.
Rapid Injection Molding, or RIM, is a way to get parts made faster through the use of molds that are easier and faster to produce. With the molds designed for lower volume production runs, how they are maintained can be the difference between having to produce a new mold, and maximizing the production value of the existing mold. As many of the molds are made from aluminum, it is critical that they be cleaned well after each run.
The cleaning products used in injection molding have gone through major changes of late. Products like Mold Brite and Zap-Ox from Nanoplas are specially formulated to effectively clean molds of various materials, and are very effective for maintaining RIM molds.
Another product that can have a significant impact on mold life is the lubricating grease used. The Nanoplas Cera-Lube Nano Ceramic Grease is a high performance lubricant that works very well and can help prolong your RIM tooling.
Finally, based on the lower volumes, an area that can make RIM tooling even more effective is mold release. There has been a lot of progress in the formulations in this area as well. The challenge with RIM is that downtime to apply mold coatings can be too long. Nanoplas now has a mold release spray called Dri-Kote that is quick drying and with good bonding to metal molds.
Getting the maximum value from your RIM tooling is critical, and the way the mold is maintained and treated can make the difference. Many shops have been using the same maintenance products for a very long time, however there are alternatives that can make a difference in your workflow and tooling.
We invite you to check out the Nanoplas family of products and let us show you how they can make a difference in your shop.
by Admin | Jul 29, 2015 | Manufacturing, Recent Posts |
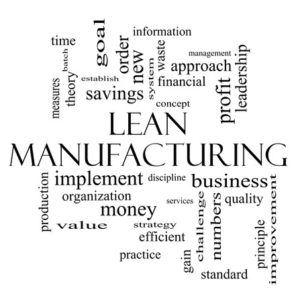
Lean Manufacturing Word Cloud Concept in black and white with great terms such as quality, discipline, concept and more.
Lean Manufacturing is often associated with a focus on cost reduction. However, through the implementation of lean manufacturing processes, many injection molders also realize reduced lead times, improved on-time delivery scores, and an increase in overall customer satisfaction.
With those types of added benefits, it’s easy to see what many shops are adopting lean principles. But what are 2 things you can do in the short term that will help you get closer to lean. 5S and Kaizen Blitz.
5S refers to five steps, namely Sort, Straighten, Shine, Standardize and Sustain, which are core to laying the foundation for continuous improvement. It is a way to systematically organize workplace to ensure it is safe and efficient.
The 5S organization concept provides an amazing boost to a lean manufacturing program, as it mandates constant checks and repairs of machinery and equipment, and it makes results immediate and notable. The results improve because of availability of required tools, properly labeled materials in their appropriate place, along with a general atmosphere of everything being in right place. There are many injection-molding companies who maximize the benefits of lean manufacturing by adopting the 5S principle.
Kaizen is a practice developed by Masaaki Imai of Japan as a way to continuously improve the workplace to make it more efficient and competitive. The various aspects of Kaizen are tackled by the whole team and involve setting up optimal processes and taking prompt actions to contain as well as resolve the actual causes of issues and problems.
A Kaizen Blitz is a concerted and focused approach to improve processes in an accelerated, expedient way. It is an intensive and rapid improvement where results are noticeable within a few days rather than over a longer period of time. In manufacturing environments, teams work together to come up with structured and creative ways to improve processes and solve problems within a short timescale.
Through the process of Kaizen Blitz, you are picking a specific area of focus. This is an important step towards progress and also gets multiple people across multiple departments and functions involved. However, the process is short yet intense by nature.
Reducing costs, and reducing waste are directly related. The lean manufacturing process can play an integral part in your competitive strategy. By implementing 5S and pursuing rapid improvements through a Kaizen Blitz concept, your shop can make real progress in a short period of time.
The Nanoplas family of products can also play an integral role in your lean approach and can also help you achieve your competitive goals. Through reduced scrap rates, improved maintenance performance and other tangible benefits, our products can make a difference across multiple areas. We invite you to contact us to learn more, and let us show you the Nanoplas difference.
by Admin | Jul 15, 2015 | Manufacturing, Plastics, Recent Posts, Uncategorized |
There is a direct correlation between having a well planned and managed mold maintenance and preventative maintenance program and realizing maximum value from your tooling investments. With the expectation that each and every part must be perfect, and that production speeds will increase, the pressure to have your tooling perform is real.
To maintain the tooling steel to perform consistently, it must have scheduled downtime for inspection, evaluation and diagnostics. It must also be cleaned and prepped using high quality mold cleaners, rust inhibitors and grease (like Nanoplas) to help ensure that mold is ready for production when needed.
In many cases, the mold cleaning and preparation process has been the same for many shops for many, many years, using the exact same products. In some cases, that may be OK, but in many cases, the advances in mold technologies and advances in mold cleaning and maintenance products can have a significant impact in the time and resources required to complete the required processes, allowing for faster change overs and less scrap in getting to acceptable part quality production.
By planning and managing a maintenance program, and evaluating and testing new products and methods for maintenance, shops can often extend the life of their tooling. To learn how Nanoplas products can benefit your injection molding operation, contact us today!
by Admin | Jul 1, 2015 | Manufacturing, Recent Posts |
Rapid Injection Molding, or RIM has really changed the plastic injection molding industry. By offering lower production quantities and quicker turnaround times, it has allowed many products to be molded versus other manufacturing methods.
One of the benefits of RIM is that most manufacturers use or follow the industry standard practices, making it a great predictor of the true manufacturability when the part moves to large-scale production quantities. By allowing for quick turns and lower quantities, buyers are able to fine tune designs and make adjustments without the huge costs of the past.
One of the ways that injection molders can make RIM even more efficient is to use a product like NanoMoldCoating from Nanoplas. This mold release coating can help with release issues on dies from the simple to the most complex. The specially formulated product uses nanotechnology to create a semi-permanent barrier on mold surfaces allowing for exceptional part release.
The Nanoplas family of products are designed to work together to make your molding operation more efficient and productive. To learn more about how NanoMoldCoating and the entire line of products from Nanoplas, contact us today!