When color isn’t evenly distributed throughout a part, appearing as streaks, swirls or patches of discolored material, you’re probably looking at color swirls. Also known as streaking, color streaks and marbling, color swirls are occasionally misidentified as black...
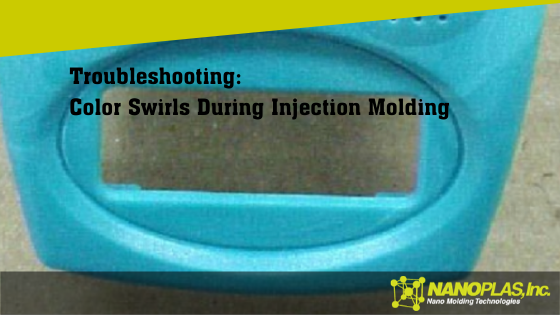