by Admin | Aug 12, 2015 | Manufacturing, Plastics, Recent Posts |
One of the challenges for injection molders is efficiency. The cycle times for plastic parts can range from 30 seconds to more than a minute. One of the primary contributors to that time and one of the longstanding constraints is cooling time. It is always a trade off of waiting for the parts to properly cool to avoid warping and shrinking, and maximizing productivity.
The concept of additive manufacturing or what used to be considered or associated with laser sintering, is a way to potentially improve the productivity and efficiency of your mold by taking advantage of conformal cooling.
The additive manufacturing process allows the toolmaker to lay down one layer of the mold at a time, creating the ability to get away from straight line drilling of cooling channels that are not as efficient. By utilizing conformal cooling channels that conform or run closer to the shape of the part allows for more efficient cooling process, and has led manufacturers to realize reduced cycle times by as much as 25-40%!
The creation of conformal cooling channels is something that must be considered when designing the tool, and is often considered an optimization task. In many of the mold software tools, are able to simulate the conformal channels, and their impact on the tool.
Making your operation more efficient is not easy. Additive manufacturing concepts for tool creation is one concept that can potentially have a very positive impact.
The Nanoplas line of mold maintenance products, and our mold coatings can also have a significant impact on your productivity levels. Contact us today to learn more about how our products can help you achieve your goals!
by Admin | Jul 15, 2015 | Manufacturing, Plastics, Recent Posts, Uncategorized |
There is a direct correlation between having a well planned and managed mold maintenance and preventative maintenance program and realizing maximum value from your tooling investments. With the expectation that each and every part must be perfect, and that production speeds will increase, the pressure to have your tooling perform is real.
To maintain the tooling steel to perform consistently, it must have scheduled downtime for inspection, evaluation and diagnostics. It must also be cleaned and prepped using high quality mold cleaners, rust inhibitors and grease (like Nanoplas) to help ensure that mold is ready for production when needed.
In many cases, the mold cleaning and preparation process has been the same for many shops for many, many years, using the exact same products. In some cases, that may be OK, but in many cases, the advances in mold technologies and advances in mold cleaning and maintenance products can have a significant impact in the time and resources required to complete the required processes, allowing for faster change overs and less scrap in getting to acceptable part quality production.
By planning and managing a maintenance program, and evaluating and testing new products and methods for maintenance, shops can often extend the life of their tooling. To learn how Nanoplas products can benefit your injection molding operation, contact us today!
by Admin | Jun 24, 2015 | Manufacturing, Plastics, Recent Posts |
Optimizing The Molding Process
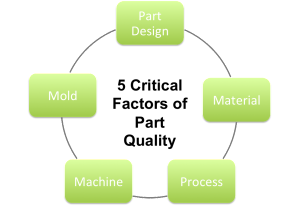
The use of Scientific Molding has had a dramatic impact on the efficiency of molding operations. The following 6 steps should be considered to help optimize the process robustness of your molding operation.
Viscosity Curve
The scientific study of viscosity curve helps show the effect produced by injection speed on viscosity, and it also shows the most consistent region of viscosity. By monitoring this data, it reduces the variation between production lots. The idea of “inject as fast as you need to and not as fast as you can” is directly related to this study, as slower speed are acceptable if allowable.
Cavity Balance Study
This aspect of the process reveals the fill balance between every cavity. It aids in the achievement of better consistency for between cavities. It facilitates studying the % imbalance and provides case-based results.
Pressure Drop Study
This study shows if the process pressure is limited, which can impact consistency. It is recommended to record pressure drop through the nozzle and at the end of fill. Recording pressure drop at other sections is important only in case of pressure-limited processes.
Cosmetic Process Window Study
This reveals the mold’s capability to form parts that are cosmetically acceptable. Technically, a large Cosmetic Process Window is the initial step towards a robust process.
Gate Seal Study
This shows the action of gate seal. It aids shot to shot consistency. However, it is not advisable to perform a Gate Seal Study on a Hot Runner Mold. Also, if the graph doesn’t flatten, it indicates time for the ‘Pack and Hold’ action.
Cooling Time Study
This aspect shows the effect of cooling time on the production. It also improves the cycle efficiency. It is also recommended to perform the study at higher end of mold temperatures.
The uses of advanced concepts in injection molding are increasing at an amazing pace. By utilizing the information from the above 6 steps, progressive molders will be better equipped to improve production efficiencies and increase throughput.
The Nanoplas’ line of injection molding products are engineered to help improve efficiencies and lower scrap rates. To learn more about how they can help your injection molding operation, contact us today!
by Nanomold Coating | Oct 2, 2014 | Manufacturing, Plastics, Recent Posts |
As one of the fastest growing scientific and engineering technologies in the world, Nanotechnology holds an incredible amount of potential, especially in the manufacturing and plastics industries. But it is also being used in fields such as bioscience, medicine, engineering, pharmacology, material sciences, and defense.
And that’s just the tip of the iceberg.
What is Nanotechnology? It involves the engineering of functional devices or systems by controlling matter on an atomic and molecular scale. Now you begin to understand the near limitless potential. Scientists now have the ability to manipulate the atomic structure of the very molecules that make up the materials in the world around us.
This enormous growth potential and set of possibilities has given industries like manufacturing exciting improvements. The very structure of materials can be changed and improved through nanotechnology. For example, the plastics industry has embraced the use of nano-materials to provide plastics with greater conductivity, increased strength, flexibility and durability, and unique surface characteristics, etc.
Other nano-scale materials can be used in thin films to make them anti-reflective, self-cleaning, ultraviolet or infrared-resistant, antifog, anti-microbial, scratch-resistant, electrically conductive, anti-stick, water-repellent and oil-repellant…the list goes on.
NanoMoldCoating
Our own NanoMoldCoating product is one of these innovative new polymer films that creates optimal solutions to most of the typical issues in injection molding. The coating dramatically increases production output, while reducing costs associated with manual part removal, costly mold release agents, part scrap, slow cycle times, and repetitive mold maintenance due to sticking problems.
It’s the ideal choice for plastics and rubber processors in today’s competitive manufacturing environment, and it taps into the incredible potential of nanotechnologies.
If you’d like to find out more about Nanotechnology or NanoMoldCoating, please feel free to contact us HERE and we’ll be glad to answer any questions you have.
by Nanomold Coating | Sep 11, 2014 | Plastics, Recent Posts |
5 Major Advantages to Using Plastic Injection Molding for the Manufacturing of Parts
Plastic injection molding is extremely versatile method of producing parts and products. It is one of the preferred methods for manufacturing parts because it has multiple advantages over other methods of plastic molding. Not only is plastic injection molding simpler and more reliable, it is also extremely efficient. You should have no doubts about using this method to manufacture parts.
Here are 5 major advantages of using injection molding for manufacturing plastic parts and components.
1. Detailed Features and Complex Geometry
The injection molds are subjected to extremely high pressure. As a result the plastic within the molds is pressed harder against the mold compared to any other molding process. Due to this excessively high pressure, it is possible to add a large amount of details into the design of the part.
Furthermore, due to high pressure during the molding process, complex and intricate shapes can easily be designed and manufactured which otherwise would have been too complicated and expensive to manufacture.
2. High Efficiency
Once the injection molds have been designed to the customer’s specifications and the presses pre-programmed, the actual molding process is very quick compared to other methods of molding. Plastic injection molding process hardly takes times and this allows more parts to be manufactured from a single mold. The high production output rate makes plastic injection molding more cost effective and efficient. Typically, hot-runner ejection mold systems produce parts with more consistent quality and do so with faster cycle times, but it’s not as easy to change colors nor can hot runners accommodate some heat-sensitive polymers. Learn more about the key differences between hot-runner and cold-runner systems.
3. Enhanced Strength
In plastic injection molding, it is possible to use fillers in the injection molds. These filler reduce the density of the plastic while it being molded and also help in adding greater strength to the part after it has been molded. In fields where parts need to be strong and durable, plastic injection has an option that other molding processes do not offer.
4. Ability to Use Multiple Plastic Types Simultaneously
One of the major advantages of using plastic injection molding for manufacturing parts is the ability to use different types of plastic simultaneously. This can be done with the help of co-injection molding, which takes away the worry about using a specific type of plastic.
5. Automation to Save Manufacturing Costs
Plastic injection molding is an automated process. A majority of the injection molding process is performed by machines and robotics which a sole operator can control and manage. Automation helps to reduce manufacturing costs, as the overheads are significantly reduced. Furthermore, with reduced labor force the overall cost of manufacturing the parts is reduced and this cost saving can easily be passed on to the customer.
Furthermore, automation allows for making precise and accurate injection molds. Computer aided design (CAD) and computer aided manufacturing (CAM) allow close tolerances during the making of the molds.
The Bottom Line
Using injection molding also ensures the parts manufactured hardly require any work after the production. This is because the parts have more or less a finished appearance after they are ejected from the injection molds.
Today, plastic injection molding is an environment-friendly process. The scrap plastic generated during the production process is reground and re-used. Hence, the process generates very little waste.
by Nanomold Coating | Aug 7, 2014 | Plastics, Recent Posts |
Plastic injection molding pressures are classified based on the clamping pressure that the molding presses exert. This is the reason why it’s important to check the size of the press, which is often referred to as the tonnage. The clamping pressure exerted by the press can range anywhere from 5 tons to more than 4,000 tons. (more…)